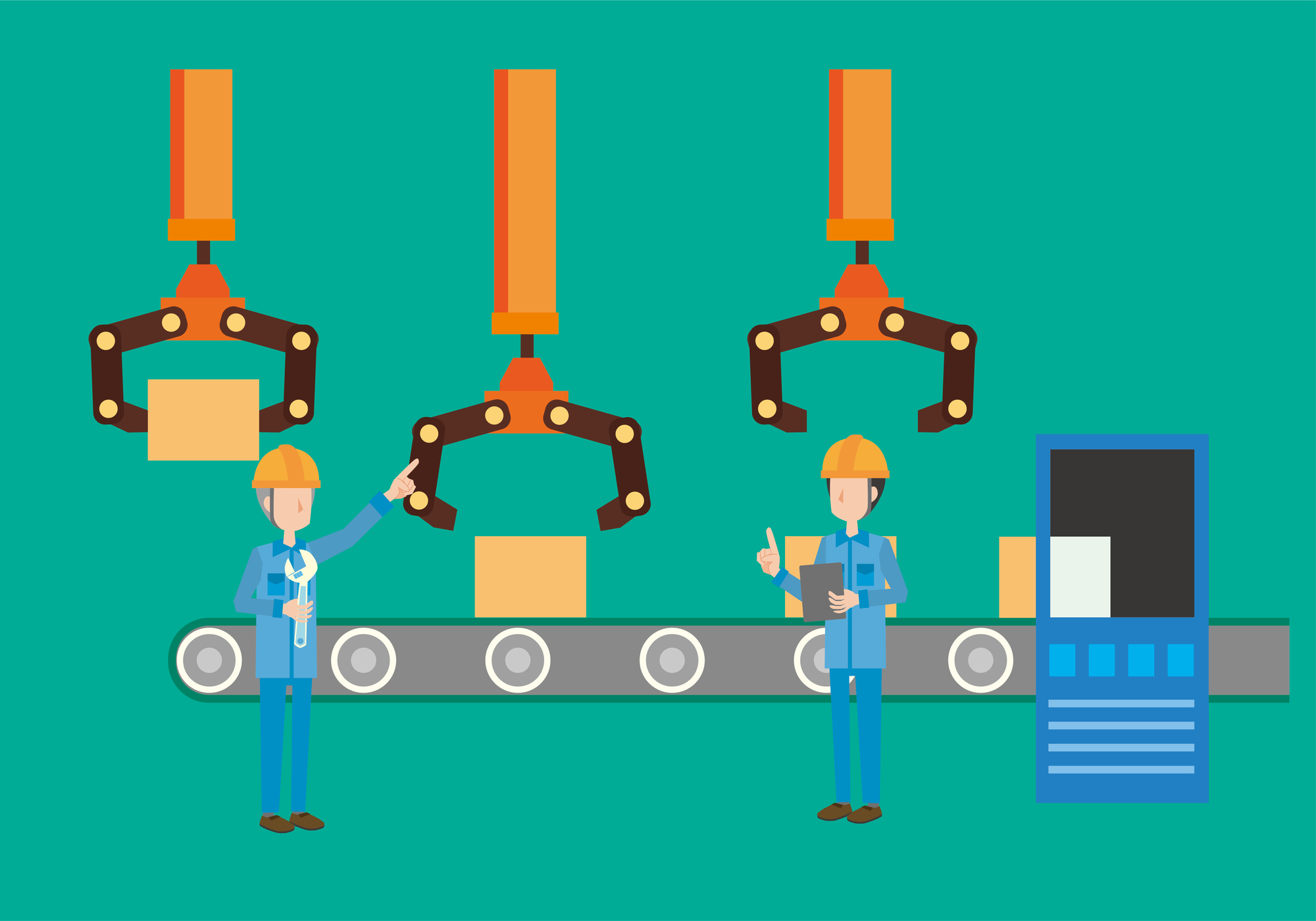
品質のばらつきや品質の不良は、あらゆる企業や組織で避けたい事態として位置づけられます。その品質のばらつきが起きる原因としては、通常と異なる工程で製造をしてしまったり、使用する機械が以前と違っていたり、さらには作業者の違いなど、その原因は多岐にわたります。
そのため、品質のばらつきを抑えるためには、やみくもに改善策を講じるのではなく品質のばらつきが一体なぜ発生するのか、その原因をしっかりと理解することが重要です。
品質の維持は企業の信頼性を高め、顧客満足度を確保するための鍵となります。だからこそ、品質のばらつきは多くの品質管理担当者の悩みになっていることでしょう。そこで本記事では、品質のばらつきの概要からなぜ品質のばらつきが生じるのか、品質のばらつきの原因に対しての解決策を詳細に解説します。
目次
品質のばらつきとは?
製品を製造する際、見た目や製品番号が全く同じであっても、微細な違いや差異が生じることがあります。これを「ばらつき」と呼びます。ばらつきは、製造工程や材料の性質、機械の精度などさまざまな要因によって生じるもので、品質管理上非常に重要な概念です。例えば、1/100mmのような極めて小さな単位での差異でも、高精度が要求される製品においては大きな問題となることがあります。したがって、製品の品質を一定に保つためには、このばらつきをできるだけ小さくすることが求められます。それを実現するための取り組みや管理が、製造業界における品質管理の核心となる部分です。
品質のばらつきの許容範囲外が不良品
製品製造における「ばらつき」は、どんな製品でも避けられない現象です。しかし、この「ばらつきがある=品質不良」とは言えません。なぜなら、製造時には「許容範囲」というものが設定されており、この範囲内でのばらつきは許容されるからです。具体的には、製品の設計段階で、ある部品の長さや重さなどの特性にどれだけのばらつきを許容するかを決め、その範囲内であれば良品として判断されます。
逆に、この許容範囲を超えてしまった製品は品質不良とされます。例えば、機械部品の寸法が設定した許容範囲よりも大きく外れてしまうと、組み立て時に適合しなかったり、動作不良を引き起こす恐れがあるため、不良品として扱われます。
このように、品質管理では「ばらつき」自体をなくすことよりも、そのばらつきが許容範囲内に収まっているかどうかを重視します。これにより、製品の品質と生産効率のバランスを保つことができます。
品質のばらつきが発生する原因
ここでは、品質のばらつきが発生する原因について解説します。
- 機械・材料による原因
- 人・環境・管理体制による原因
- 手順・検査による原因
- 業務の属人化による原因
それでは、1つずつ解説します。
機械・材料による原因
品質のばらつきが発生する原因の1つ目は、機械・材料による原因です。
特に、使用する機械や材料の種類が増えると、その影響で品質のばらつきも大きくなります。機械に関しては、故障や経年劣化が原因で微妙なばらつきが生じることがあります。例えば、注ぐ液体の量が一定でなかったり、仕上げの厚みが均一でない場合などが挙げられます。また、機械の部分的な交換や異なる機械での作業代替など、生産設備の変更が行われると、新たなばらつきの原因が生じることがあります。
一方、材料の場合、供給元の変更や使用する材料の種類の変わり目は、ばらつきの原因となりやすいです。例えば、供給先が原料を変更していたり、同じ製品と認識していても実際には生産地が異なっている場合など、予期せぬばらつきが生じることがあります。このような原因を把握し、適切に対応することが品質管理の鍵となります。
人・環境・管理体制による原因
品質のばらつきが発生する原因の2つ目は、人・環境・管理体制による原因です。
まず、人の原因としては、新人や経験が少ない作業者は、ミスや作業のムラが出ることがあります。また、人の心身の状態、睡眠不足や体調不良、精神的ストレスも品質のばらつきを招く原因となります。
環境的な原因では、日本のように季節の変化が激しい国では、温度や湿度、気圧などの変動が製品に影響を及ぼすことがあります。これに対する適切な対策が求められます。
最後に、管理体制の変動もばらつきの原因となり得ます。生産計画の変更や人員の増減、勤務体制の変動、指導方法の見直し等は、製品の一貫した品質を維持する上では弊害となることがあります。例えば、シフト制による異なる作業者の入れ替えや研修方法の変更は、生産の均一性を乱す原因となることが考えられます。これらの要因を適切に管理し、品質の一貫性を保つことが重要です。
手順・検査による原因
品質のばらつきが発生する原因の3つ目は、手順・検査による原因です。
マニュアルや手順書の資料が不十分だったり、最新情報に更新されていなかったりすると、品質の均一性が損なわれるリスクが高まります。例えば、機械の入れ替えや新しい効率的な手法が導入された場合、それらが手順書に反映され、正しく作業者へと指導されていない場合、人によって作業方法の差異が生じ、品質にばらつきが出てしまいます。
さらに、検査段階でばらつきが発生することがあります。例えば、検査機器の不具合や検査手法のブレが生じると、製品の評価が一定しなくなります。結論として、品質管理を正確に行うためには、適切な手順書の整備とその実践、そして正確な検査が不可欠です。
業務の属人化による原因
品質のばらつきが発生する原因の4つ目は、業務の属人化による原因です。
「業務の属人化」とは、特定の個人に業務のノウハウや経験が集中し、その人がいないと業務がスムーズに進行しない状態を指します。このような状態では、その個人の技術や知識、経験に大きく依存するため、他の人が同じ業務を担当した場合、品質にばらつきが生じやすくなります。
さらに、属人化している業務では、その人独自の作業手順や判断基準が存在する可能性があり、これが正式なマニュアルや手順とは異なる場合があるため、結果として品質の均一性が損なわれることが考えられます。
関連記事:属人化を徹底解析!メリットと解消して標準化する方法を解説
品質のばらつきを解決する方法
ここでは、品質のばらつきを解決する方法について解説します。
- グラフなどを活用し分析
- 機械の点検・清掃
- 材料の品質再検査
- 人材の配置換え
- マニュアル・研修の実施
- 社内wikiによるナレッジ共有
それでは、1つずつ解説します。
グラフなどを活用し分析
品質のばらつきを解決する方法の1つ目は、グラフなどを活用し分析することです。
品質管理は、製品やサービスの品質を一定以上に保つための活動ですが、その実践において極めて重要な役割を果たすのがデータの収集、整理、そしてグラフなどを活用した分析です。これらのデータを効果的に扱うための基本的な手法として、「QC7つ道具」が知られています。なお、QCは、品質管理を意味するQuality Controlの略です。
QC7つ道具は、7つの基本的なグラフや図を用いて、品質の問題点やその要因を可視化・分析するためのツール群です。具体的には、パレート図、ヒストグラム、特性要因図、散布図、チェックシート、グラフ、管理図などがこれに該当します。
これらのツールは、製造現場で起こる様々な問題やその背後にある要因を明確にし、改善活動の方向性を決定するのに役立ちます。例えば、パレート図は、問題の主要因を特定するのに適しており、特性要因図は問題の原因を洗い出すのに有効です。
このように、QC7つ道具は、品質問題の「見える化」や原因の特定、そして改善策の策定に大変有用な手法として、品質管理の現場で広く利用されています。
機械の点検・清掃
品質のばらつきを解決する方法の2つ目は、機械の点検・清掃です。
機械に関連するばらつきの解消策として、初めに考えられるのは機械のメンテナンスです。定期的な点検や整備はもちろん、日常の清掃や摩耗部品の交換サイクルの管理が不可欠です。これにより、機械の性能を一定に保ち、不具合や急な故障を予防できます。
さらに、製造工程の中で多くの工程が連携して動いている場合、上流工程での微小な問題が、下流で大きな影響を及ぼすことがあります。これを避けるため、全工程を通じた点検や確認を丁寧に実施することが必要です。
また、機械の正確な操作方法や最新の機能についての理解は、作業者の習熟度と密接に関連します。機械メーカーからの再教育や研修を受けることで、作業者のスキルアップを図り、機械由来の品質ばらつきを最小限にすることが期待されます。
材料の品質再検査
品質のばらつきを解決する方法の3つ目は、材料の品質再検査です。
品質を確保するため、材料の品質再検査を実施して材料自体に問題がないかを確認します。また、再検査だけでは不十分な場合、直接仕入先へヒアリングを行うことも考えられます。
仕入先の方から品質変更の情報が伝わっていない、あるいは品質に変動があった場合、対応策としてはいくつかの選択肢が考えられます。最も基本的なのは、仕入先に対して元の品質に戻すよう要請することです。しかし、それが難しい場合や、再び同じ問題が起きるリスクを回避したい場合、別の仕入先を検討することも一つの手段となります。
さらに、新しい材料や代替材料への移行を考える場合もあります。新しい材料を使用することで、既存の材料の問題を回避し、品質の安定化を図ることができます。ただし、新材料への切り替えには十分な検証や試験が必要となります。
人材の配置換え
品質のばらつきを解決する方法の4つ目は、人材の配置換えです。
人材の配置換えとは、作業者の役割や担当業務を見直し、最適なポジションに再配置することを指します。これにはいくつかの理由や目的があります。まず、作業者の特性や能力に合わせた業務割り当てです。人はそれぞれ得意・不得意や経験、知識が異なります。それを考慮し、それぞれの強みを最大限活用できるポジションに配置することで、品質の安定化や生産性の向上を図ることができます。
次に、技術や知識の伝承・継承の観点からです。ベテランと新人を同じ班やチームに配置することで、ベテランの経験やノウハウが新人に伝わり、スキルの均一化や技術の継続が期待されます。そして、モチベーションの面からも新しい業務や環境にすることで、作業者のモチベーションを向上させ、それが品質向上につながることもあります。
マニュアル・研修の実施
品質のばらつきを解決する方法の5つ目は、マニュアル・研修の実施です。
マニュアルの整備は、業務手順や操作方法を標準化し、文書化することで、作業者間の取り扱いの差異を最小限に抑えるためのものです。特に、複雑な作業や経験や勘を頼りに行われがちな作業においては、マニュアルが明確なガイドラインとして機能します。このようなマニュアルが存在することで、新人や異なる部署からの異動者も迅速に業務を習得することが期待できます。
研修の実施は、マニュアルに記載されている内容を実践的に学ぶ場を提供することで、理論と実践のギャップを埋める役割を果たします。研修では、実際の作業を模倣したり、ベテラン職員からの直接の指導を受けることで、より実践的な知識や技術の習得が促進されます。
社内wikiによるナレッジ共有
品質のばらつきを解決する方法の6つ目は、社内wikiによるナレッジ共有です。
社内wikiは、従業員が日常の業務中に得た知識や経験を簡単に記録・共有するための内部用の情報共有プラットフォームです。社内wikiの特徴として、情報の追加や更新が手軽で、検索機能を通じて必要な情報を即座に引き出すことができる点が挙げられます。
品質のばらつきは、知識や経験の共有が不十分な結果、作業者間での情報の非対称性に起因することが多いです。こうした背景から、社内wikiを活用することで、ベテランのノウハウや特定の作業者だけが知っているような情報を共有することで品質のばらつきを解消することが可能です。
関連記事:社内版ウィキペディア「社内wiki」とは? ほかの情報共有ツールとの違い、使い分け方を徹底解説
まとめ
本記事では、品質のばらつきの概要・発生する原因・解決する方法について解説してきました。品質のばらつきとは、製品やサービスの中で均一性が確保できていない状態を指します。品質のばらつきが多いと、不良品や顧客の不満が生まれるリスクが高まります。そのため、企業の競争力を保つ上でも品質管理は絶えず続ける必要があり、そのためのツールやシステムを導入することで、より効率的に問題を特定・解決する必要があります。品質のばらつきをなくすことで、顧客満足度の向上やコスト削減にも繋がりますので、今すぐ社内wikiやマニュアルを活用し、品質の向上を目指しましょう。
NotePM(ノートピーエム) は、Webで簡単にマニュアル作成できて、強力な検索機能でほしい情報をすぐに見つけられるサービスです。さまざまな業界業種に導入されている人気サービスで、大手IT製品レビューサイトでは、とくに『使いやすいさ・導入しやすさ』を高く評価されています。
NotePMの特徴
- マニュアル作成、バージョン管理、社外メンバー共有
- 強力な検索機能。PDFやExcelの中身も全文検索
- 社内FAQ・質問箱・社内ポータルとしても活用できる
- 銀行、大学も導入している高度なセキュリティ。安全に情報共有できる
URL: https://notepm.jp/